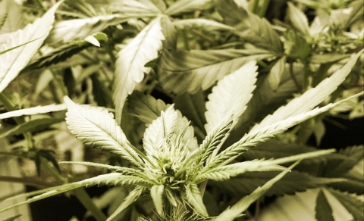
Introduction
One of the largest reoccurring expenses growers are faced with is the ever-increasing cost of energy. Average electricity cost varies wildly across the country with some jurisdictions paying as much as $0.31 per kilowatt-hour (Hawaii) and others paying as little as $0.07 per kilowatthour (Louisiana)(i). The impact this has on the bottom line is self-evident. A typical grower providing 12 hours of supplemental lighting to a 300-light glasshouse will see electricity bills exceeding $200,000 per year(ii).
This impact has led many growers to consider a transition to energy efficient solid-state (LED) lighting to reduce energy consumption and lower costs. In many states, the transition is being mandated to reduce the stress on the electricity grid and lower greenhouse gas emission associated with electrical power generation(iii). California’s CASE Initiative 2022 has called for the elimination of all HID grow lights by 2023.
A simple comparison, on a light-by-light basis, shows that a 1000W DE HPS grow light costs $1.85 per day on average, while a comparable LED grow light costs under $1.00 to operate.
The challenge is to lower energy consumption, thereby lowering operating costs, without sacrificing plant health and yield. Selecting the right supplemental light source is a critical step to assuring continued production efficiencies.
Where we fit in
The CT141 LED fixture is designed to replace energy-hogging HPS fixtures in commercial greenhouse environments. CT141 incorporates a patented, tunable daylight analog spectrum that provides the appropriate amount of light for the majority of cultivars grown in modern greenhouses while providing over 40% total energy savings. The natural white light supplements the available daylight seamlessly. All these technological advancements mean that
greenhouses replacing HPS lights with CT141 LED fixtures will have an immediate impact on operational costs (OPEX).
Energy Savings
Simple energy saving calculations show that replacing a 1080-watt fixture with a 600-watt fixture will provide energy savings of 44.5% on lighting alone. This does not consider the additional savings provided by a reduced refrigeration load or the potential increases in heating costs in colder operating months.
Example Case Study
Location: Plymouth, MA Square Footage: 24,050 Crop: Medicinal Cannabis Legacy Technology: 436 1000W DE HPS Cost per Kilowatt-hour: $0.24
Parameter | LED | HPS |
---|---|---|
Total Fixtures | 436 | 436 |
Annual per Fixture kWh | 2,523 | 4,730 |
Total Annual kWh | 1,099,976 | 2,062,454 |
Total Cost | $263,994.16 | $494,989.06 |
Total Savings | $230,994.89 | – |
The annualized savings demonstrated in the audited case study provided a first-year energy savings of $230,000 dollars attributed solely to the replacement of the HPS lights with CT141 LEDs(iv). Total annual operating cost per light fixture (excluding maintenance) dropped from $1,135.30 to $605.49 per fixture.
The total annual BTU load was reduced from over 7B BTUs to under 3B BTUs as well. As the overall BTU load is reduced due to removal of the heat generating HPS lamps, there is also a reduction in the venting of the greenhouse roof vents, which improves the CO2 enrichment of the space. The increased efficiency of the CO2 utilization creates a more consistent environment for growing operations, leading to greater yield and even more financial gain.
Additional savings can be obtained by implementing daylight harvesting technologies to hit day light integral (DLI) values. This concept implements seamless dimming to supplement light levels to precise set points by reading current ambient light and only providing enough supplement to hit grower defined DLI targets.
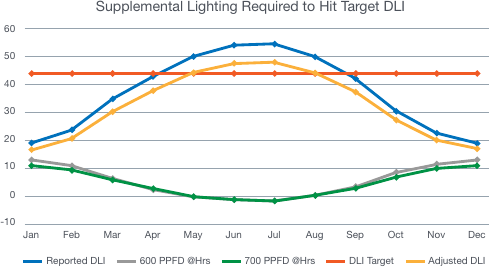
As demonstrated in the above chart, the adjusted DLI available in the greenhouse by month can be supplemented with specific PPFD levels to hit a target DLI. When there is adequate light to achieve DLI targets the lights can be automatically dimmed or turned off. In this example, no supplemental lighting is required from May through August, and the gentle slope of supplemental lighting requirements can be auto adjusted to provide just the right amount of supplement. This strategy, not possible with legacy HPS lighting, further reduces energy load, resulting in savings that exponentially add onto the initial savings from a one-for-one transition to LED from HPS(v).
Another significant benefit is the ability to tune the spectrum to more closely replicate or enhance the existing ambient light. In the past, many growers would use a “checkerboard matrix” of both HPS and MH lights to supplement the “blue” and “red” portions of daylight. With CT141, growers can achieve both blue and red dominant peaks, adjusting spectral content for individual cultivars’ specific photometric preferences and requirements.
Reduction in Maintenance Costs
The typical HPS grow light requires a minimum of an annual lamp change, and to ensure efficacy, the cleaning of reflector components. With LED grow lights, users are assured a 5-year maintenance free installation. LEDs do not require light source swaps or special cleanings to retain their overall efficacy.
Lifetime efficacy is conveyed in an L90 expression. L90 is the amount of time a fixture takes to reach 90% of initial output. With the standard HPS lamp, the 90% of initial output is achieved after as little as 4000 hours (one year of operation at 12 hours per day). LED grow lights do not fall below the 90% threshold until >36,000 hours. When fixtures begin producing less light, that equates to less photosynthetic activity, lower yields, and less profitable harvests.
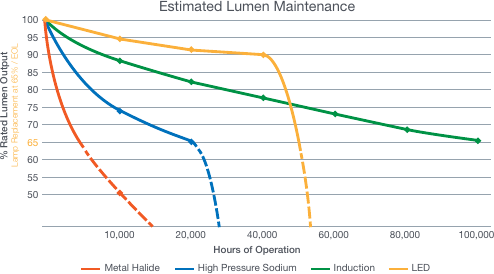
During the audited case study referenced above, it was determined that, while policy stated annual lamp swaps, this maintenance was not being performed consistently. Bulbs were only swapped upon failure, and PAR readings were not consistently used as the impetus for changing lamps. The results were a measurable yield reduction, year over year. The transition to LED has provided crop yield consistency and lower overall cost.
HPS Bulb Cost | $73.95 |
Replacement Frequency | Annual |
Annual Bulb Cost | $32,242.20 |
Five Year Bulb Cost | $161,211.00 |
Long-Term Savings
With a robust warranty available for most LED grow lights, calculating long-term savings is simple math:
(Annual Energy Savings x Warranty Period) + MRO Savings = Life-Time Savings
In our example, annual energy savings amounted to $230,994.89, and with a 5-year warranty this totals $1,154,974.46 in energy savings in that time frame. Accounting for proper HPS bulb swaps, an additional $161,211.00 was projected to be saved, totaling $1,316,185.46 in savings over 5 years. More savvy financial professionals would also calculate rising cost of energy, inflation, carrying cost, and environmental impacts.
In this case study, the facility saved 962,479 kWh. According to the EPA, this equates to a 682 metric ton reduction in Carbon Dioxide(vi). Beyond the benefit of monetary savings, the reduction in overall environmental impact cannot be overlooked.
As growers transition to LED lighting systems, greenhouse budgets benefit from more than the initial energy savings of one-to-one HPS replacement. We’ve discussed several key financial factors when projecting the long-term savings of LED replacement.
- The transition from HPS lighting to LED lighting yields immediate cost savings. In the example case study provided, energy usage reduced by nearly 47% in the first year.
- Advanced LED dimming technology (featured in CT series luminaires) improves daylight harvesting capabilities, further reducing energy consumption over time.
- Growers can rely on a singular LED fixture with advanced spectral technology to achieve both red and blue dominant peaks, eliminating the need to stock both HPS and MH lights.
- LED fixtures can operate for much longer than HPS lights before dropping below 90% operating threshold. Longer lasting brightness translates to greater yield for crops.
- Transitioning to LED lighting eliminates the need for bulb swaps over the fixture’s lifetime. In the provided case study, $161,211 would be saved over the course of 5 years on bulb replacement (the length of warranty of the Fotono LED fixture).
- While many potential savings are difficult to measure (improved CO2 efficiency increasing crop yield, reduced refrigeration load, rising cost of energy over time, etc.), in the audited case study, the facility is projected to obtain $1,154,974.46 in savings over the course of 5 years.
- Of course, the potential cost savings of replacing HPS with LED will vary by operation. To begin calculating the potential ROI of an LED transition, contact the team at cabatech.com/grow.